Dzisiaj publikujemy trzeci wpis przygotowany przez Martę Norenberg poświęcony samodzielnemu wykonaniu końcówek do rzemieni, bransolet i naszyjników.
Serdecznie zapraszamy do działania, a także do odwiedzenia strony www Artystki oraz fanpage’a.
To już trzecia wersja końcówek, jakie chciałabym Ci pokazać. Tym razem zajmiemy się wykończeniem prac o prostokątnych końcach. Tego typu zaślepka idealnie nadaje się do płaskich, szerokich rzemieni oraz beadingowych bransolet (także tych robionych na krośnie).
Plusy i minusy
Dzięki umiejętności wykonania prostokątnych końcówek nie będziesz ograniczony do tego co oferują sklepy z półfabrykatami. Marzy Ci się szeroka bransoleta, ale brakuje zakończeń o tym wymiarze? Nie ma problemu, zrobisz je sobie sam drogi Czytelniku. Jest tylko jeden drobny szkopuł, tym razem nie odnajdziesz gotowych elementów, które Ci w tym pomogą jak było to w przypadku okrągłych zakończeń wykonanych z rurki. Wierzę jednak, że jest w Tobie sporo chęci do nauki czegoś nowego.
Materiały / narzędzia
- srebrna / miedziana / mosiężna blacha (wedle uznania). Grubość blachy od około 0.7 mm – 1.0 mm będzie wystarczająca.
- srebrny drut fi 1.5 mm (nie jest niezbędny, wszystko zależy od wybranej metody działania, z tych które opisałam poniżej)
- Standardowe materiały potrzebne przy działaniach jubilerskich:
- lutownica gazowa albo palnik na propan – butan,
- suwmiarka,
- ramka do cięcia (gesztelka) i piłki włosowe (rozmiar 3/0) lub nożyce do blachy,
- lutówka,
- ogniotrwały podkład,
- lut srebrny LS 70 / Ag700 (średnia twardość),
- pęseta,
- kwasek cytrynowy do wykwaszania,
- miska z wodą do studzenia,
- pilnik o nr 3 lub 4 i drobne pilniki – iglaki,
- papier ścierny,
- opcjonalnie mini szlifierka ręczna i końcówki wedle uznania,
- różnego rodzaju szczypce (najlepiej szyncęgi, czyli cęgi płasko – półokrągłe),
- szczypce tnące,
- młotek ślusarski (najbardziej typowy)
- młotek drewniany
- twardy podkład (np. kowadełko).
Zaczynamy
Na początku bardzo przydatny jest gotowy element, do którego wykonujemy zakończenie (dla ułatwienia będę go nazywać rzemieniem, ale w Twoim przypadku może to być np. koniec bransolety). Musisz go dokładnie wymierzyć, szczególnie szerokość i grubość. Głębokość końcówek zależy od Twojego widzimisię, ale pamiętaj że nie mogą być zbyt płytkie (po wklejeniu rzemień może się wysunąć), ani za głębokie (wtedy będą niewygodne dla noszącego).
Zaczynamy od wykonania profilu, który będzie stanowił pionową ściankę końcówki, czyli grubość naszego rzemienia. Pamiętaj, aby końcówkę zrobić minimalnie większą niż rzemień. Ów profil wystarczy jak będzie 0.5 mm wyższy od rzemienia, dzięki czemu znajdzie się w nim miejsce na klej.
Mam dla Ciebie trzy metody wykonania tego profilu:
1. BLACHA. Możesz wyciąć z blachy pasek odpowiedniej szerokości i długości. Najlepiej jeśli użyjesz do tego ramki i piłek włosowych. Dzięki temu blacha się nie pognie, jak przy cięciu nożyczkami. Do tego blacha powinna mieć grubość ok 0.8 – 1.0 mm, ponieważ z cieńszą będzie Ci się później trudno pracować, a końcówka może wyjść zbyt delikatna.
UWAGA: do długości profilu dodaj podwojoną grubość blachy, której użyjesz. Czyli jeśli chcesz wyciąć kawałek o długości 5.0 cm, a blacha ma grubość 1.0 mm, to wytnij odcinek o długości 5.0 cm i 2.0 mm. Później wytłumaczę, po co Ci ten zabieg.
2. DRUT. Możesz wykorzystać drut np. o średnicy 1.5 mm, wygrzać go pod płomieniem, wykwasić i ostudzić. Tak przygotowany drut uderzaj płaską stroną młotka na twardym / stalowym podkładzie (kowadle). Musisz pilnować zarówno siły uderzeń, jak i uzyskanej grubości profilu. Po wymłotkowaniu dobrze jest wygładzić metal papierem ściernym i dopiero wtedy odmierzyć żądaną długość.
3. GRUBY DRUT. Tą metodę zastosowałam przy moich końcówkach. Posiadałam gruby drut (5.0 mm średnicy) próby 925, wygrzałam go i ostudziłam. Do jego wydłużenia i rozpłaszczenia użyłam walcarki (fot. 1), czyli urządzenia przypominającego pralkę Franię.
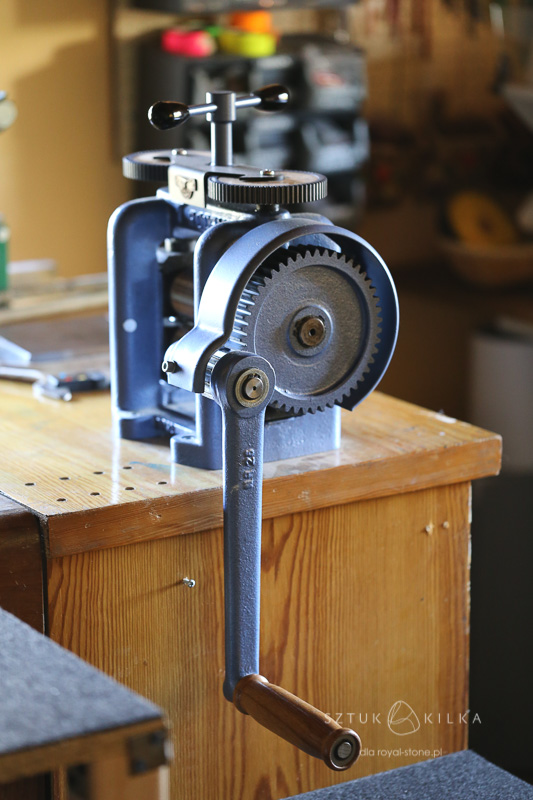
Moja walcarka posiada dwa walce, których powierzchnia jest podzielona na dwie strefy: płaską i z sześciobocznymi rowkami, nad nimi znajduje się pokrętło do zwiększania nacisku walców (fot. 2).
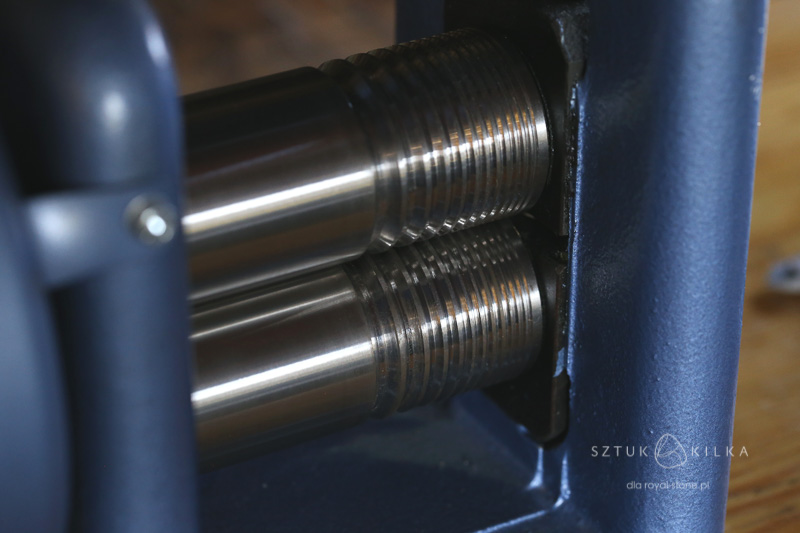
Natomiast z boku jest rączka do kręcenia walcami. Zasada jest bardzo prosta, jeśli chcę uzyskać dłuższy i węższy drut, to przewalcowuję go przez coraz mniejsze rowki (im jest węższy, tym w przekroju bardziej przypomina kwadrat). Po osiągnięciu odpowiedniej grubości drutu jeszcze raz go wyżarzam, aby odzyskał swą miękkość i wtedy przepuszczam go przez płaskie walce, uzyskując w ten sposób płaski pasek blachy. Wszystko widać na zdjęciach, to cały czas jest ten sam kawałek srebra, a zobacz jak bardzo się wydłużył (fot. 3-5). UWAGA: walce trzeba zaciskać stopniowo, jeśli zbyt mocno je ściśniemy, to możemy uzyskać zbyt cienki kawałek blachy, który do niczego się nam nie przyda (fot. 3-6).
Gdy już mamy nasz profil, czas odmierzyć kawałki (najlepiej użyj do tego suwmiarki). Przy odrysowywaniu upewnij się, że masz równy brzeg blachy, do którego przykładasz suwmiarkę. W przeciwnym wypadku wszystko wyjdzie Ci skośne (fot. 7). Moje końcówki będą niesymetryczne, co widać po wyznaczonych liniach (fot. 8). W miejscach zaznaczenia każdej ze ścianek wykonaj piłką delikatne nacięcie, dosłownie 1-2 pociągnięć piłką, trzymaj ramkę poziomo, jak na zdjęciu i tnij “do siebie” (fot. 9). Teraz będziesz potrzebować niedużego, kwadratowego pilnika. Krawędzią pilnika piłuj miejsce nacięcia w kierunku od siebie (fot. 10). W tym miejscu powinno powstać trójkątne wgłębienie. Powtarzaj piłowanie, aż rowek będzie sięgał do połowy grubości profilu (fot. 11).
W miejscu rowków będziesz zaginać swój profil, dlatego pamiętaj, że przy zbyt głębokich nacięciach metal może pęknąć, a przy zbyt płytkich narożniki wyjdą zaokrąglone, a nie ostre (fot. 12). Do zagięcia profilu najlepsze będą najzwyklejsze płaskie cążki. Pamiętaj, aby przed gięciem wygrzać metal i raz zagiętego elementu nie odginać, bo może pęknąć. Właśnie ze względu na owe zaginanie potrzebne były nam te dwa dodatkowe milimetry, inaczej końcówka wyszłaby nam minimalnie mniejsza od zamierzonego rozmiaru.
Po zagięciu elementów narożniki najlepiej zlutować, nie jest to konieczne, ale wzmacnia konstrukcję. Zagięte profile połóż na ogniotrwałym materiale, narożniki posmaruj lutówką i ułóż na nic drobinki lutu LS 70 (średniej twardości). Delikatnie i równomiernie nagrzej metal tak, aby lut nie odskoczył, aż do momentu gdy lut popłynie. Wykwaś, opłucz i wysusz elementy. Istnieje jeszcze drugi sposób lutowania, dla osób troszkę wprawionych w bojach. Zamiast kłaść kawałeczki lutu przy rurce ucinam większy kawałek i łapię go w samozaciskowe szczypce. Przedmiot rozgrzewam i gdy nabierze odpowiedniego „gorącego odcienia” dotykam lutem w miejscu styku metali (fot. 13), a on w tym momencie topi się i płynie wokół linii łączenia.
Teraz musisz zlutować kątowniki z płaską blachą, utnij kawałki blachy trochę większe od profili. W ten sposób łatwiej będzie Ci nagrzać całość. Lut potnij sobie na drobne kawałeczki, wielkości ok 2-3 mm, posmaruj miejsce łączenia lutówką i ułóż na niej pałeczki lutu (fot. 14). Delikatnie rozgrzewaj element, na początku tylko muskaj metal płomieniem, aż lutówka wyschnie. W dalszej kolejności możesz troszkę mocniej nagrzać blachę, aż zauważysz, że lut się stopił. Po lutowaniu wrzuć element do wykwaszania i sprawdź czy się dobrze zlutował. Jeśli nie, to powtórz ten krok jeszcze raz (gdyby wkoło detalu pozostało dużo lutu, to nie dodawaj więcej, tylko posmaruj lutówką i przygrzej jeszcze raz całość). W ten sposób uzyskaliśmy tylną ściankę końcówki (fot. 15).
W tym kroku odcinamy nadmiar blachy, możesz do tego użyć piłki jubilerskiej lub nożyc, następnie szlifujemy wszystkie krawędzie, aż końcówki będą gładkie (fot. 16). Teraz możemy już przystąpić do lutowania przedniej ścianki. Kroki działania są identyczne, jak w punkcie nr 6. UWAGA: aby ułatwić sobie pracę, to przy lutowaniu profilu do blachy możesz ustawić go przy krawędzi, wtedy tej jednej nie będziesz musiał wycinać (fot. 17).
Jeszcze raz po upewnieniu się co do dokładności lutowania obcinamy nadmiar blachy i szlifujemy całość (fot. 18 – 20). Końcówki są już prawie gotowe, zostało jedynie dorobienie oczka. Do jego wykonania wykorzystałam resztę profilu , z którego zrobiłam boczne ścianki.
Wygrzałam profil i za pomocą szyncęg (szczypce płasko – półokrągłe) ukształtowałam łuk, dopiero wtedy odcięłam element i wyszlifowałam (fot. 21).
Łuk ułożyłam tuż przy końcówce i miejsca łączeń pokryłam lutówką, od góry położyłam kawałeczki lutu (fot. 22-23).
A teraz lutujemy! Niezbyt mocnym płomieniem delikatnie podgrzałam konstrukcję tak, aby lutówka wyschła. Na tym etapie bardziej grzałam końcówkę, ponieważ dolutowywane oczko, mogłoby się zbyt szybko nagrzać i stopić. Gdy końcówka była już nagrzana zaczęłam muskać płomieniem łuk, aż do stopienia lutu. Gorący przedmiot wrzuciłam następnie do kwasku cytrynowego w celu wykwaszenia.
Po wykwaszeniu i osuszeniu elementów potraktowałam ich powierzchnię gruboziarnistym papierem ściernym (gradacja 150) dla uzyskania delikatnej faktury (fot. 24) . Możesz także wykorzystać końcówkę z włókniny (fot. 25). W tym drugim przypadku uzyskasz powierzchnię satynową.
Efekt końcowy
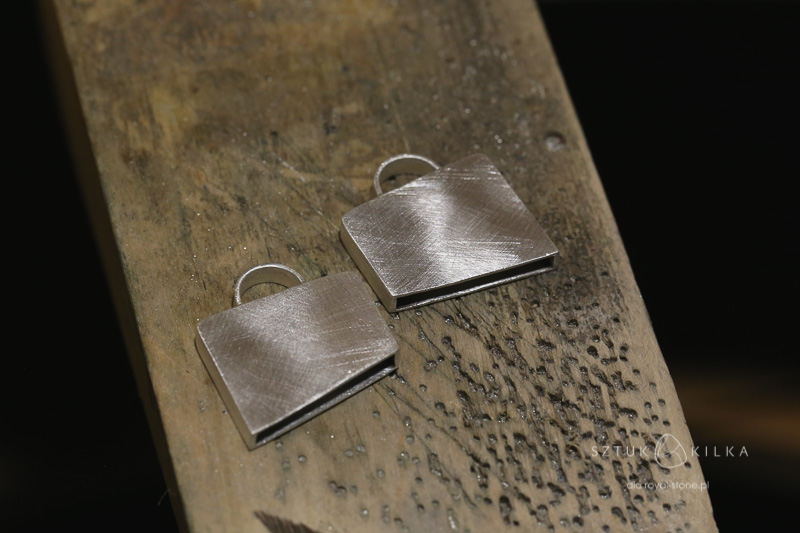
Pozdrawiam cieplutko
Leave A Comment